Introduction to PLC
Programmable Logic Controllers (plc) are a key component in the rapid development of industrial automation, which has enabled businesses to become more efficient and productive.
This versatile and powerful technology has transformed the way industries manage their processes, providing numerous advantages to businesses in a variety of industries.
This blog post will provide an overview of the functions, applications, and advantages of PLCs, as well as how they are influencing the future of automation.
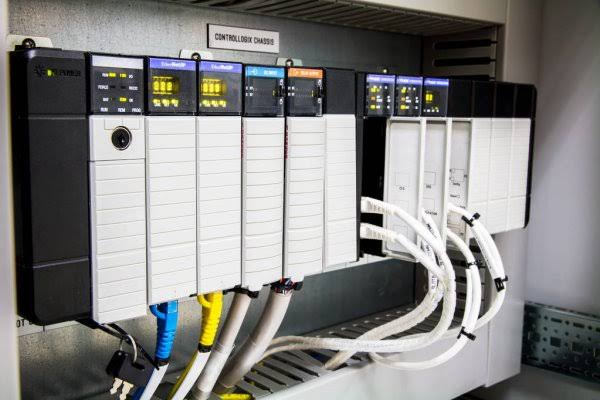
Understanding Programmable Logic Controller (PLC) in instrumentation
A Programmable Logic Controller, commonly referred to as PLC, is a digital computing device designed to manage and control machinery and processes in industrial settings. Programmable Logic Controllers are programmable and can be easily customized to meet specific automation requirements. These controllers can handle a wide range of tasks, from simple relay logic operations to complex algorithms and data processing.
Programmable Logic Controllers have evolved significantly since their inception, moving from fixed-function relay systems to sophisticated microprocessor-based units. Their ability to execute tasks rapidly, accurately, and repeatedly has made them indispensable in manufacturing, automotive, pharmaceuticals, food processing, and various other industries.
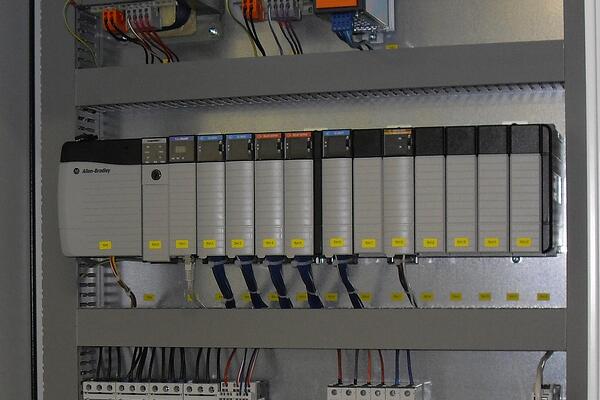
The Functions and Features of Programmable Logic Controllers (PLCs)
2.1. Logic Operations: The fundamental role of a Programmable logic controller is to execute logical operations based on the inputs received from sensors and other devices. The Programmable Logic Controller’s program defines these logical operations, making it possible to control machines and processes effectively.
2.2. Memory and Processing: Programmable logic controllers have two types of memory – data memory and program memory. Data memory stores values and variables used during program execution, while program memory contains the set of instructions to be executed. Programmable logic controllers process the instructions sequentially, ensuring precise control over the connected machinery.
2.3. Communication: Modern Programmable logic controllers are equipped with communication capabilities, enabling them to interact with other devices, systems, or even cloud-based platforms. This feature enhances data exchange, remote monitoring, and real-time control.
2.4. Modularity and Expandability: Programmable logic controllers are designed to be modular, allowing users to add or remove I/O modules and other components as per their requirements. This flexibility ensures that the controller can adapt to changing automation needs.
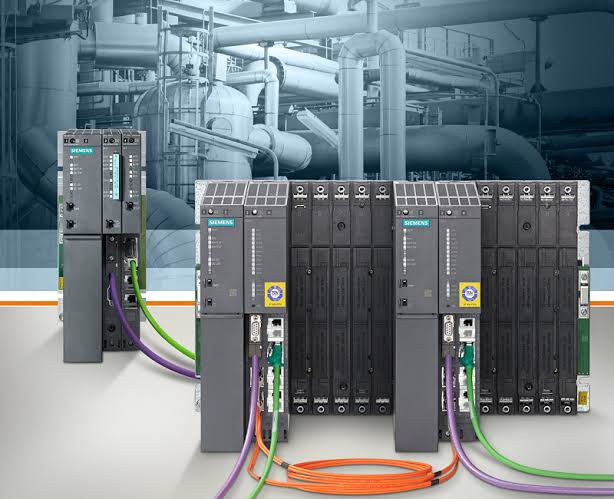
Applications of Programmable Logic Controller (PLCs)
3.1. Manufacturing and Assembly Lines: Programmable logic controllers play a pivotal role in manufacturing industries by controlling assembly lines, robotic arms, and conveyor systems. They enable precise coordination, fault detection, and process optimization, leading to increased productivity and reduced downtime.
3.2. Process Control: Programmable logic controllers are extensively used in industries with continuous processes, such as chemical plants, oil refineries, and water treatment facilities. They monitor and regulate variables like temperature, pressure, and flow, ensuring safe and efficient operations.
3.3. Building Automation: Programmable logic controllers are employed in building management systems for tasks like climate control, lighting, security, and access control. They help optimize energy consumption and create a comfortable environment for occupants.
3.4. Transportation and Logistics: Programmable logic controllers are utilized in traffic management systems, railway signaling, and airport baggage handling systems to ensure smooth and safe transportation operations.
3.5. Energy Management: Programmable logic controllers aid in optimizing energy consumption in industries by controlling motors, pumps, and lighting systems based on demand and usage patterns.
Advantages of Programmable Logic Controllers (PLCs)
4.1. Flexibility and Customization: Programmable logic controllers can be easily programmed and reprogrammed to adapt to different processes and production requirements. This versatility allows industries to implement changes quickly and efficiently.
4.2. Reliability: Programmable logic controllers are known for their robustness and reliability. They are designed to withstand harsh industrial environments, ensuring continuous operation with minimal maintenance.
4.3. Faster Response Times: Programmable logic controllers execute instructions with exceptional speed, making them ideal for applications where quick responses are critical, such as safety shutdowns and emergency controls.
4.4. Cost-Effective: Despite their advanced capabilities, Programmable logic controllers are cost-effective solutions for industrial automation compared to traditional relay-based control systems.
4.5. Diagnostics and Troubleshooting: Programmable logic controllers offer comprehensive diagnostics and monitoring features, facilitating proactive maintenance and quick troubleshooting.
Conclusion
To sum up, PLCs have revolutionized the industrial automation landscape. Their capacity to simplify processes, increase productivity, and guarantee accurate control have made them a key component of modern industrial sectors.
From manufacturing, process control, building management, and transportation, PLCs (Programmable Logic Controllers ) are continuing to play a significant role in the shaping of automation in the future. As technology advances, it is likely that PLCs will continue to lead the way in innovation, enabling industries to reach new levels of efficiency and sustainability.
Our You tube Channel Our Facebook page