In the intricate world of process industries, where accurate measurement of fluid flow is paramount, flowmeters emerge as unsung heroes. These devices play a crucial role in ensuring efficiency, safety, and precision in various applications, from manufacturing plants to oil refineries. In this comprehensive guide, we will delve into the intricacies of flowmeters, exploring their types, working principles, applications, and the evolving landscape of flow measurement technology.
Understanding Flowmeters
Flowmeters are fluid flow meters, whether they are liquid flowmeters or gas flowmeters.
The main function of a flowmeter is to measure the amount of fluid flowing through a particular point in the system. This data is very important for controlling processes, ensuring quality control, and optimizing the overall system.

Types of Flowmeters
Differential Pressure Flowmeters:
- The Venturi Meter and Orifice Plate are common examples. These flowmeters work on the principle that the pressure drop across a constriction in the flow path is related to the flow rate.
Velocity Flowmeters:
- Turbine and electromagnetic flowmeters fall into this category. They measure the velocity of the fluid directly, which is then used to calculate the flow rate.
Positive Displacement Flowmeters:
- Devices like piston meters and oval gear meters belong to this type. Positive displacement flowmeters trap and measure a specific volume of fluid, providing highly accurate readings.
- Mass Flowmeters: Coriolis flowmeters and thermal mass flowmeters operate based on the mass flow rate of the fluid, ensuring accuracy even when the fluid properties change.
- Ultrasonic Flowmeters: Utilizing ultrasonic waves, these flowmeters measure the time it takes for sound waves to travel with and against the flow, providing a non-intrusive and versatile solution.
Working Principles
Differential Pressure Flowmeters: These flowmeters rely on the principle that the pressure drop across a constriction is proportional to the square of the flow rate. This pressure drop is then correlated to the flow rate.
- Velocity Flowmeters: Turbine flowmeters, for example, use the rotation of a turbine in the fluid stream to calculate the velocity and, consequently, the flow rate.
- Positive Displacement Flowmeters: These flowmeters trap and measure a specific volume of fluid, providing a direct measurement of the flow rate.
- Mass Flowmeters: Coriolis flowmeters measure the deflection of a vibrating tube caused by the mass flow of fluid. Thermal mass flowmeters, on the other hand, rely on the cooling effect of a fluid stream to determine its mass flow rate.
- Ultrasonic Flowmeters: Ultrasonic flowmeters use the transit time of ultrasonic pulses to calculate the velocity of the fluid, offering a non-intrusive and reliable measurement method.
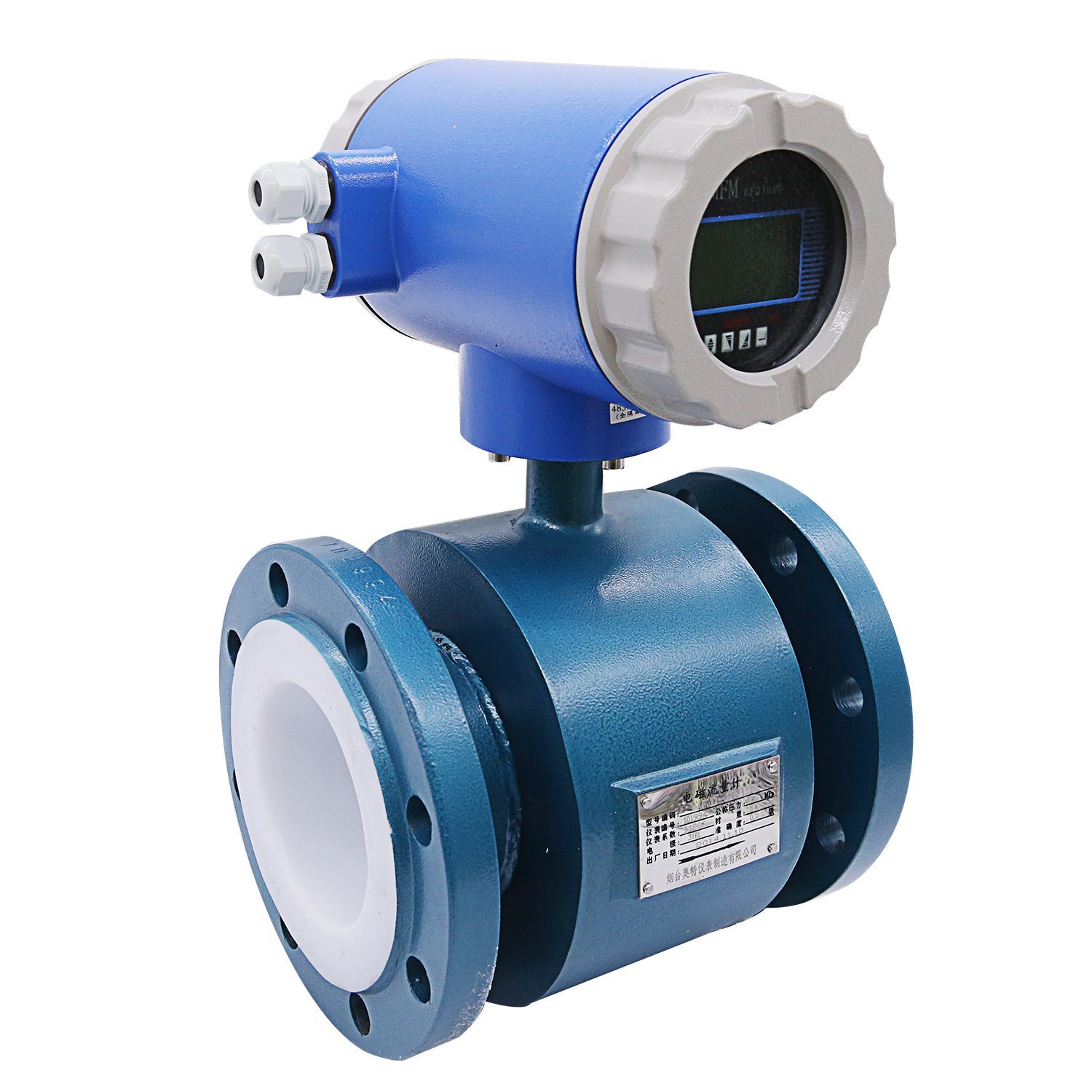
Applications of Flowmeters
Oil and Gas Industry:
Flowmeters are extensively used in measuring the flow rates of crude oil, natural gas, and refined products, ensuring accurate custody transfer and efficient production processes.
Chemical Processing:
Flowmeters play a crucial role in monitoring and controlling the flow of various chemicals, ensuring precise mixing and maintaining product quality.
Water Treatment and Distribution:
In water treatment plants, flowmeters help in monitoring the flow of water and chemicals, optimizing the treatment process and ensuring compliance with regulatory standards.
Food and Beverage Industry:
From measuring ingredients in the production process to monitoring the flow of liquids in bottling plants, flowmeters are integral to maintaining consistency and quality in the food and beverage industry.
Pharmaceutical Manufacturing:
Flowmeters contribute to the accurate dosing and mixing of pharmaceutical ingredients, ensuring the quality and efficacy of the final products.
The Evolving Landscape: Smart Flowmeters
In recent years, the integration of technology has transformed traditional flowmeters into smart devices that offer enhanced functionalities and connectivity.
Smart flowmeters often come equipped with features such as remote monitoring, data logging, and real-time analytics. These capabilities allow for better control and optimization of processes, predictive maintenance, and improved overall efficiency.
Furthermore, the Internet of Things (IoT) has facilitated the integration of flowmeters into larger industrial networks.
With the ability to communicate with other devices and systems, smart flowmeters contribute to the concept of Industry 4.0, where automation and data exchange drive manufacturing processes to new heights of efficiency.
Conclusion
In the vast landscape of process industries, flowmeters stand as indispensable tools for ensuring precision, efficiency, and reliability.
From traditional differential pressure flowmeters to cutting-edge smart devices, the evolution of flow measurement technology continues to shape the way industries operate.
As we navigate the complexities of fluid dynamics in diverse applications, understanding the types, principles, and applications of flowmeters becomes crucial for engineers, technicians, and professionals in the field.
With advancements in technology, the future promises even more sophisticated and integrated solutions, reaffirming the role of flowmeters as key instruments in the pursuit of operational excellence and sustainability in various industries.
Home Page Our You Tube Channel