Introduction
If you’re an Instrumentation Engineer, Instrumentation Technician, or just want to learn more about this important part of control valve, this article is for you!

In the vast world of process control, control valve stand as the guardians of precision.
Control valves are a vital part of any industrial system and are responsible for controlling the flow, pressure and volume of various liquids.
In this step-by-step guide, we’ll cover everything you need to know about control valves and how instrumentation technicians can help you get the most out of them.
In other words, we’re going to talk about what it’s like to work with an instrumentation technician, the unsung hero of their operation.
1. Understanding Control Valves
A control valve is an automatic device used to regulate the flow of fluid, gas, and steam in a system. A control valve acts as a modulator, changing the rate of flow in response to a process controller’s signal.
Control valves are available in a variety of types, such as globe valve, butterfly valve, ball valve, and plug. Each type has its own application and characteristics.
Instrumentation technicians play a crucial role in selecting the appropriate control valve for a specific process, considering factors such as flow requirements, pressure ratings, and material compatibility.
2. How Control Valves Work ?
At its core, a control valve operates on a simple principle – it alters the flow of fluid by varying the size of the flow passage through which the fluid travels. This is achieved through an actuator that responds to signals from a process controller. The instrumentation technician’s role comes into play during the installation, calibration, and maintenance phases of the control valve’s lifecycle.
3. Working Principles of Control Valves
Control valves operate based on different principles, such as the linear motion of the sliding stem or the rotary motion of the quarter-turn valve. The position of the valve plug or disc, influenced by the actuator, determines the flow rate.
Instrumentation technicians must be well-versed in the inner workings of these valves, including pneumatic and electronic actuation systems, to troubleshoot and calibrate them effectively.
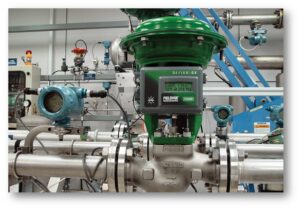
4. Control Valve Sizing and Selection
One of the most important factors in process control is the control valve size. If the valve is too small, the pressure will drop too much, and if the valve is too large, the control resolution will not be as good as it could be.
In order to determine the correct control valve size, the instrumentation engineers & instrumentation technicians must calculate the flow rate, pressure drop, and other parameters.
Additionally, they need to consider the compatibility of materials and the process fluid to avoid corrosion and other potential issues.
5. Installation and Calibration
If you want your control valves to work properly, you need to make sure they’re properly installed and calibrated.
That means instrumentation technician needs to make sure the valves are in the right place, set up correctly, and supported properly.
Also, they need to make sure the positioner is set up correctly to get the control you want.
Control valve calibration has come a long way with the help of digital valve positioners, as well as smart valve technology, which allows technicians to get better diagnostics and up-to-date data for better performance.

6. Maintenance and Troubleshooting
Regular maintenance is vital to keep control valves in peak condition and prevent unexpected failures. Instrumentation technicians must establish a maintenance schedule that includes cleaning, inspection, and testing. They should also look out for potential issues like valve stiction, excessive leakage, and valve packing problems.
When troubleshooting control valves, technicians employ various tools like valve signature analysis, positioner diagnostics, and loop tuning techniques to identify and resolve issues promptly.
7. The Role of an Instrumentation Technician
An instrumentation technician is a skilled professional responsible for the proper functioning of control valves and other process instruments. Their tasks involve:
a. Installation and Commissioning: Technicians ensure the correct placement and integration of control valves within the system. Precise installation is crucial to prevent inaccuracies and potential safety hazards.
b. Calibration: Regular calibration of control valves is vital to maintain accuracy and consistency in process control. Technicians use specialized tools and techniques to ensure the valve responds appropriately to control signals.
c. Troubleshooting and Maintenance: When control valves malfunction, an instrumentation technician is the first line of defense. They diagnose issues, perform repairs, and conduct preventive maintenance to extend the valve’s lifespan and prevent costly downtime.

8. Instrumentation Engineering for Control Valves
Instrumentation engineering is a specialized branch that focuses on designing, developing, and maintaining control systems and instruments. Instrumentation engineers work closely with technicians to ensure control valves integrate seamlessly into the overall control system. They also play a role in selecting the appropriate valve type based on the process requirements and system conditions.
9. Conclusion
Control valves are the heart of any process control system, ensuring precision and efficiency in industrial processes. Instrumentation technicians are the skilled professionals who play a vital role in the proper selection, installation, calibration, and maintenance of these critical devices.
With their expertise in control valve technology and instrumentation, these technicians are the unsung heroes who keep industries running smoothly. By continuously expanding their knowledge and adapting to the latest advancements, they can master the art of control valves and drive the future of process automation.
Home Our Face Book Page Our You tube Channel