In this post we will discuss the common faults that may occur in a pneumatic valve in instrumentation. Valves play an important role to control the industrial processes.
Common faults can include:
1. Stiction:
Stiction is when the plug or disc of the valve sticks or has a lot of friction inside the valve, making it hard for it to move around. It can make the valve slow down, take longer to open, or not respond correctly to control signals.
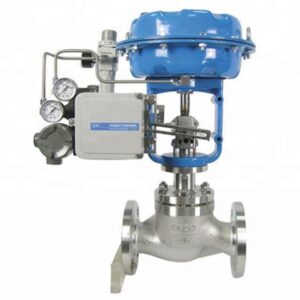
2. control valve Seat leakage:
When the valve stops working properly when it’s closed, it can cause the seat to leak. This can happen because the valve seats are damaged or worn, the seat is not properly installed, or there’s not enough force to close the valve.
This can lead to a loss of control over the process, a decrease in efficiency, and even a safety hazard.
3. Actuator problems:
Control valves are typically equipped with actuators that provide the necessary force to move the valve plug or disc. Actuator faults can include issues such as air supply problems, malfunctioning solenoids, faulty positioners, or incorrect actuator sizing. These faults can result in poor valve control, erratic movement, or inability to maintain desired positions.

4. Erosion and corrosion:
Valves handling fluids with high velocities or corrosive properties can experience erosion and corrosion, which can degrade the valve components over time. This can lead to loss of sealing, decreased flow capacity, or even structural failure.
5. Instrumentation faults:
Control valves are often part of a larger control system that includes sensors, transmitters, controllers, and other instruments. Faults in the instrumentation, such as faulty wiring, sensor drift, or communication errors, can impact the performance and reliability of the control valve.
Detecting and diagnosing faults in control valves often requires a combination of visual inspection, performance monitoring, and testing.
Techniques such as pressure and leakage testing, signal analysis, and calibration checks can help identify specific faults and their underlying causes. Once a fault is identified, appropriate corrective actions can be taken, which may include repair or replacement of faulty components, reseating or resealing the valve, or adjusting the control system parameters.
Our Face book Page Our You tube Channel