Introduction:
Control valves are useful components in various industries, from oil and gas to manufacturing and beyond. They play a vital role in regulating fluid flow, pressure, temperature, and level within a system. In this post we will discuss some important interview questions and answers. This post is also very helpful, If your are preparing for instrumentation interview questions.
Control valve interview Questions for instrumentation Technician & Engineer
To help you get started, we’ve put together a list of the most common interview questions and how to answer them.
Whether you’ve been in the industry for years or are just starting out, these questions will help you feel comfortable and confident in your next technician or engineer interview.
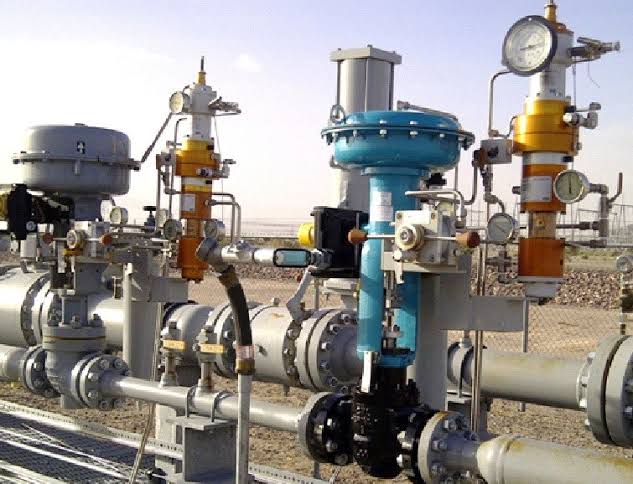
1. What is a control valve, and how does it work?
A control valve is a device that modulates the flow of fluids or gases to maintain desired process parameters.
It typically consists the following
a valve body,
an actuator,
and a positioner.
The valve body controls the fluid flow.
the actuator positions the valve based on the control signal.
and, the positioner ensures accurate valve positioning.
The process fluid passes through the valve body, and the actuator adjusts the valve’s opening or closing to achieve the desired setpoint.
2. What are the different types of control valves?
a) Globe Valves: Provide good throttling control and are commonly used in applications requiring fine adjustments. Globe valve is used for precise control. The shape of globe valve is like a globe.
b) Butterfly Valves: Ideal for large flow applications where fast response is necessary. Butterfly valve is used for on/off control. In ball valves a ball is used to control the flow. the shape of ball valve is like a ball.
c) Ball Valves: Suitable for on/off control and less ideal for throttling.
d) Diaphragm Valves: Used for precise control of corrosive or abrasive fluids.
e) Rotary Plug Valves: Excellent for high-pressure drop applications and offer good controllability.

3. What factors should be considered while selecting a control valve ?
The selection of a control valve depends on several factors, These factor are:
– Process parameters (such as flow rate, pressure, temperature)
– Valve type and size
– Material compatibility with the process fluid
– Valve characteristic (linear, equal percentage, quick opening)
– Actuator type (pneumatic, electric, hydraulic)
– Control system requirements
4. Explain the term control valve Cv (Flow Coefficient) of a valve .
It is an important question.
Cv is a measure of a control valve’s flow capacity.
It represents the flow rate of water in gallons per minute (GPM) that a valve can pass with a pressure drop of 1 psi across the valve.
A higher Cv indicates a larger flow capacity.
The formula to calculate Cv is
Cv = Q / (ΔP × √SG),
where Q is the flow rate, ΔP is the pressure drop, and SG is the specific gravity of the fluid.
5. What is the significance of valve trim?
Valve trim is the part of the control valve that comes into contact with the flow of the process fluid. It consists of the plug, the seat, and other components that control the flow of the fluid.
Selecting the right valve trim can have a significant impact on a variety of parameters such as flow, pressure reduction, and erosion resistance.
6. How do you determine the appropriate valve size for a given application?
The valve size is determined based on the required flow capacity and pressure drop.
instrumentation Engineers often use sizing equations or control valve selection software provided by manufacturers to find the suitable valve size for a specific application.
7. What are the different control valve actuators, and how do they differ?
Common valve actuators include:
– Pneumatic Actuators: Use air pressure to position the valve, suitable for fast and reliable operations.
– Electric Actuators: Utilize electric power for precise control and automation.
– Hydraulic Actuators: Use hydraulic fluid to position the valve in large and high-pressure applications.
8. How can cavitation and flashing impact control valve performance?
Cavitation is when the pressure drops below the vapor pressure of the liquid, causing it to bubble and collapse.
Flashing is when a liquid that was at high pressure turns into low-pressure vapor when it goes through a valve. Both of these can damage the valve, making it harder to control and causing a lot of noise.
9. How do you troubleshoot control valve problems in the field?
Troubleshooting control valves involves a systematic approach.
This includes-
checking for air leaks in actuators.
inspecting valve trim for damage or wear.
verifying signal provided to valve.
and, ensuring proper calibration of the positioner.
Regular maintenance and timely replacement of faulty parts are essential.

10 What is the significance of flow characteristic in a control valve?
A: The flow characteristic determines how the valve responds to changes in the control signal.
A linear flow characteristic provides a proportional flow rate change for a given change in the valve position, while an equal percentage flow characteristic provides a logarithmic response, which is commonly used for processes with non-linear relationships between the control signal and the desired process variable.
Our Facebook Page